Das Globe in Coburg – eine Kulturstätte aus Holz und Beton
Auf dem Gelände des ehemaligen Güterbahnhofs im Süden der Stadt Coburg wird derzeit ein neues Kapitel in der Coburger Stadtentwicklung geschrieben. Das sogenannte „Globe“ wird dabei zum Herzstück des Areals werden. Es wird während der mehrjährigen Generalsanierung des Landestheaters in Coburg als Ersatzspielstätte dienen. Anschließend soll es für Kultur- und Bildungsveranstaltungen dauerhaft genutzt werden.
Das „Globe“ wird in Holz-Hybrid-Bauweise erstellt, wobei die Baustoffe Holz und Beton die statischen Lasten übernehmen. Die Hülle und die Innenwände des Hauptgebäudes werden in Holzmassivbauweise und die drei Nebengebäude komplett in Holzskelettbauweise gefertigt. Das Rohmaterial stammt dabei aus nachhaltig bewirtschafteten Wäldern. Das Kellergeschoß und die Treppenhäuser werden aus Stahlbeton gefertigt, Teile der Geschoßdecken bestehen aus Brettsperrholz-Beton-Verbundelementen. Tragwerksplaner Dr.-Ing. Jonas Schmidt von der Ingenieurgruppe Knörnschild & Kollegen ist Projektleiter für das Holzbauprojekt „Globe“. Im Interview spricht er über die technische Konstruktion und die Besonderheiten des Gebäudes aus planerischer Sicht.
„Es fängt im Untergeschoss mit einer wasserundurchlässigen Betonkonstruktion inkl. Frischbetonverbundfolie für hochwertige Nutzung an. Ab der Kellerdecke ist der Hauptwerkstoff – bis auf zwei Stahlbetontreppenhäuser – das Holz. Ein planerisches Highlight ist das Druck-Zugring-System, bei dem sich das Dach nach innen gegenseitig abstützt. Auch das unterspannte Dachtragwerk über dem Saal ist eine schöne Konstruktion. Eine Herausforderung, insbesondere hinsichtlich des Schwingungsverhaltens, sind die bis zu 4 Meter auskragenden Holz-Beton-Verbunddecken – eine Hybridbauweise, bei der die Stärken der einzelnen Werkstoffe Holz und Beton kombiniert werden. Dabei werden vom Holz überwiegend Zug- und vom Beton überwiegend Druckkräfte aufgenommen. Die Schubkraftübertragung der übereinander angeordneten Werkstoffe wird beim Globe über eine Verschraubung mittels Würth FT-Verbindern realisiert.“
Wachstumstreiber der Zukunft
Das Projekt berücksichtigt verschiedene Trends und verdeutlicht die Wachstumstreiber der Zukunft: Holzbau und nachhaltiges Bauen. Ein zentraler Baustein ist die Bauweise mit Holz als nachwachsendem und CO2-bindendem Rohstoff. Durch die Verwendung von Betonfertigteilen für die Holz-Beton-Verbunddecken wird die Bauzeit verkürzt. Außerdem wird keine zusätzliche Feuchtigkeit in den Baukörper eingetragen, wie es bei Ortbeton der Fall wäre. Die Betonteile werden im Werk mitsamt den Würth FT-Verbindern vorgefertigt und auf der Baustelle mit den Holzbauteilen statisch wirksam verschraubt. Dabei kommen ca. 28.000 Würth ASSY® Schrauben zum Einsatz. Durch diese Bauweise entfällt die Trocknungszeit und die Decken sind nach Herstellung des Verbundes direkt belastbar. Zudem punktet die Holz-Beton-Verbundbauweise mit hoher Tragfähigkeit und gutem Schwingungsverhalten.
Verarbeitung der Fertigteile mit Würth FT-Verbindern auf der Baustelle
Während bei den „konventionellen“ Systemen immer der nasse Ortbeton auf die Holzkonstruktion aufgebracht werden muss, bietet dieses System hier die Möglichkeit, die Betonplatte getrennt vom Holzbau vorzufertigen. Die vorgefertigten Betonplatten werden, wie man es vom Massivbau kennt, auf die Baustelle transportiert, dort auf der Holzkonstruktion verlegt und mit dieser nachträglich vor Ort verschraubt. Zum Transport der vorgefertigten Betonteile kommt eine 4-Punkt-Befestigung inklusive lastverteilender Traverse zum Einsatz. Die in der Armierung verankerten Transportschlaufen werden nach der Verlegung der Elemente entfernt.
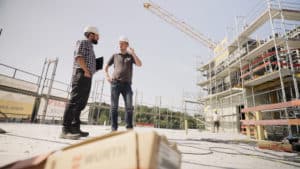
Der nachträgliche Verbund zwischen Beton und Holzkonstruktion stellt sich unmittelbar mit dem Setzen der Schrauben ein. Aufwändiges Abstützen der Deckenkonstruktion bis zum Abbinden des Betons entfällt hier vollständig. Zur Sicherstellung des Kontaktschlusses zwischen Betonplatte und Holz werden zusätzlich konstruktiv senkrechte Würth ASSY® Teilgewindeschrauben auf der Oberseite des Betons angeordnet.
Die Montage der einzelnen Konstruktionsstücke kann unmittelbar nacheinander erfolgen. Aushärtungs- und Trocknungszeiten entfallen. Durch die Vorfertigung der Elemente kommt es zu keinem Feuchtigkeitseintrag und zu keiner Verschmutzung der Holzbauteile durch Wasserausscheidungen des Betons. Eine Trennlage zum Schutz des Holzes ist hier nicht erforderlich.
„Diese BAUWEISE IST EINE PREMIERE FÜR UNS ALLE“
Tragwerksplaner Dr.-Ing. Jonas Schmidt von der Ingenieurgruppe Knörnschild & Kollegen ist Projektleiter für das Holzbauprojekt „Globe“ in Coburg. Im Interview erklärt er, warum das Prestigeprojekt für ihn nicht nur eine technische Herausforderung, sondern auch eine Herzensangelegenheit ist.
Herr Schmidt, Sie haben mehrere Lehraufträge an der Hochschule Coburg und unterrichten u. a. die Fächer Stahlbau und Sonderthemen des Holzbaus. Welche Rolle spielt die Hochschule beim Projekt „Globe“?
Dr.-Ing. Jonas Schmidt (JS): Die Entwurfsidee für den runden Theaterbau aus Holz stammt von zwei Studierenden der Hochschule Coburg. Die Pläne wurden dann durch das Architekturbüro Glodschei modifiziert, aber im Kern ist es ein Projekt, das seinen Anfang in der Hochschule nahm.
Für die Realisierung haben auch die drei Coburger Firmen HUK Coburg, Brose und Kaeser Kompressoren Geld gegeben – rund drei Millionen Euro. Ein typisches Beispiel für regionale Netzwerkstärke?
JS: Ja, das muss man sagen. Ohne das Engagement der lokalen Unternehmen wäre das Projekt nicht ins Rollen gekommen. Wir haben hier eine sehr gute Zusammenarbeit mit der Stadt, der Hochschule, starken lokalen Geldgebern und ausführenden Firmen erlebt. So ist es letztlich auch möglich, ein derartiges Prestigeprojekt zu erstellen.
Die Hybrid-Bauweise wurde in Coburg mit Betonfertigteilen realisiert. Wie funktioniert das genau und was sind die Vorteile?
JS: Der Vorteil dieser Bauweise ist, dass kein Schmutz und keine Feuchtigkeit in das Gebäude kommen. Die Fertigteile können vorgefertigt, schnell montiert und danach direkt begangen werden. Gerade die runde Bauweise ist für die Fertigteilherstellung eine große Herausforderung. Meine Neugier war groß, denn diese Bauweise war eine Premiere für uns alle – und ich muss sagen, ich bin begeistert!
Hat diese Bauweise mit Fertigteilen und vormontierten Fertigteilverbindern aus ihrer Sicht Zukunft? JS: Ja, diese Bauweise bietet die Möglichkeit der schnellen und qualitativ hochwertigen Vorfertigung. Trotz der nicht ganz einfachen Geometrien war die Verlegung sehr schnell und problemlos. Bei der Bauweise in Verbindung mit der Herstellung und Montage sehe ich somit Vorteile in wirtschaftlicher und ökologischer Hinsicht. Angesichts der Anforderungen ans nachhaltige Bauen sehe ich hier Potenziale. Dass ein großer Montagespezialist wie Würth diese Bauweise in den Fokus stellt und dafür planerischen Support bietet, macht es sicher interessant.
Werden Sie als Coburger zur Premiere kommen, wenn im „Globe“ die erste Aufführung ansteht?
JS: Ich weiß nicht, ob da ein Ticket für mich abfällt. Aber ganz sicher werde ich mir diesen Bau hin und wieder anschauen und die Konstruktion sowie jedes Detail auf mich wirken lassen.
„EINE MENSCHLICH UND FACHLICH SEHR GUTE ZUSAMMENARBEIT“
Jonas Knecht ist Bauleiter bei ZÜBLIN Timber, einem der renommiertesten Bauunternehmen für konstruktiven Holzbau. Im Interview erzählt er, was das Projekt „Globe“ in Coburg besonders macht und warum er die Zusammenarbeit mit Würth schätzt.
Herr Knecht, Sie leiten ausschließlich Bauprojekte im konstruktiven Holzbau. Warum Holz?
Jonas Knecht (JK): Mein Opa hatte eine Zimmerei, in der ich schon als Kind viel mitbekommen habe. Die Arbeit mit Holz hat mir schon immer gefallen, darum war es klar, dass ich auch beruflich mal etwas mit Holz mache. Ich habe dann eine Ausbildung zum Tischler gemacht, war ein Jahr als Tischler in Australien und habe dann meinen Holztechniker im Holzbau gemacht. Diese Kompetenz bringe ich seit einigen Jahren als Bauleiter bei ZÜBLIN Timber ein.
Welche großen Projekte haben Sie schon geleitet und was waren die Herausforderungen?
JK: Ein großes Holzbauprojekt war der Umbau des Gare Maritime in Brüssel. Hier wurden in den historischen Bahnhofshallen zwölf vier- bzw. fünfgeschossige Gebäude in reiner Holzkonstruktion errichtet. In den 12 Monaten Bauzeit wurden ca. 9.000 m³ Holz verbaut – ein spannendes Projekt! Da hatten wir übrigens mehrere Würth BAULOC Magazine im Einsatz, die alle bis oben hin mit Schrauben und anderen Materialien gefüllt waren.
Nun sind Sie seit einigen Monaten in Coburg, im Norden Bayerns und betreuen mit „Globe“ eines der spannendsten Holzbauprojekte in Deutschland. Worum handelt es sich?
JK: Das „Globe“ ist ein Theater, ein Rundbau mit auskragenden Zuschauerrängen, der zu weiten Teilen in Holzbauweise erstellt wird. Für mich neu ist die Bauweise mit Betonfertigteilen als Decken, bei der ja Würth die im Beton eingegossenen FT-Verbinder und das Montagematerial liefert. Nachdem wir nun damit fertig sind, kann ich sagen: Das ist eine überzeugende Bauweise und war insgesamt eine menschlich und fachlich sehr gute Zusammenarbeit.
Das Besondere beim „Globe“ ist also, dass hier die Verbindung Holz/Beton nicht mit Ortbeton gemacht wird, sondern mit vorgefertigten Betonteilen, in die bereits Verbinder eingegossen sind. Wie waren ihre Erfahrungen?
JK: Für uns war es das erste Mal, dass wir das so gemacht haben. Es kamen 40 Platten pro Etage, alle genau vorgefertigt – und dann ist es schon erstaunlich, wie schnell und sicher die Montage vonstattenging. Ohne, dass Feuchtigkeit durch die Verarbeitung von Ortbeton ins Bauwerk eingetragen wurde.
Die Bauweise wurde von Würth mit entwickelt. Welche Rolle spielt Würth für Sie in der täglichen Arbeit?
JK: Durch die Würth BAULOC Magazine auf den Baustellen ist immer alles sicher und zuverlässig vor Ort, was wir zur Montage benötigen. Dazu kommt eine sehr gute Betreuung und Unterstützung bei Planungsfragen. Die Ingenieure von Würth arbeiten uns zu. Das passt!
Das „Globe“ ist ja, wenn es fertig ist, auch ein bisschen ihr Baby. Werden Sie zur Premiere kommen?
JK: Seien wir ehrlich, als Bauleiter bist du ein Wanderarbeiter. Wenn hier der Auftakt zum ersten Konzert stattfindet, werde ich schon auf einer anderen Baustelle dirigieren. Aber natürlich werde ich das Projekt verfolgen und nach Möglichkeit auch mal besuchen, wenn es fertig ist. Das ist schon ein besonderes Projekt. Hier sagen zu können, da kenne ich jedes Detail und jede Schraube, das habe ich mit erbaut, das erfüllt mich mit Stolz!
Weitere Informationen zum Projekt sowie zur Holz-Beton-Verbundbauweise erhalten Sie auf www.wuerth.de/ingenieure.